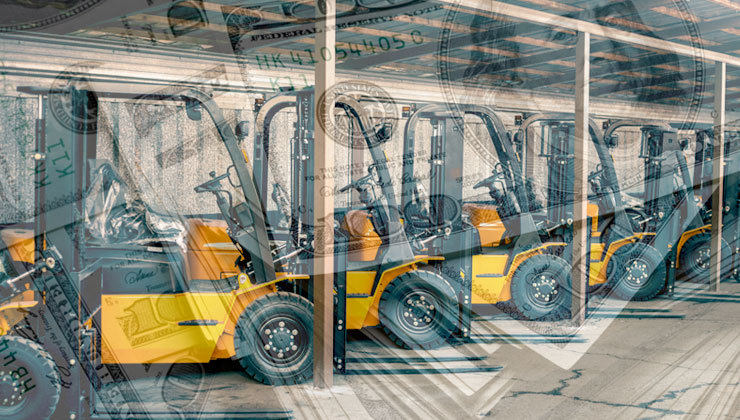
When it comes to running an efficient warehouse, it’s important to know how the expenses break down. It’s hard to reduce spending or optimize costs if you’re not exactly sure where your money is going.
Fleet vehicles likely account for a large percentage of expenses. With repairs, maintenance, and parts, each vehicle can cost several thousand dollars per year to run properly. Without knowing numbers, knowledge of money spent and how to improve can be difficult.
Many organizations, however, do not know what the unit cost of each fleet vehicle is. And that’s a problem.
Knowing the unit cost of each fleet vehicle — across all locations — gives a consolidated view of what you’re spending and where. With this data in hand, you can make critical business decisions, like whether or not to replace a truck in your fleet.
Figuring Out Service Costs
One of the main expense categories for each fleet vehicle is service—including parts and repair costs. In an ideal world, your trucks and material handling equipment would run perfectly forever, but we know that’s not always possible. Unfortunately, service costs are a harsh reality of owning a fleet vehicle.
Parts can wear out over time, and it takes a skilled technician to diagnose and repair the problem correctly. Tracking service costs for each vehicle will give you an idea of where the money is going.
By doing this, you’ll get additional insight on which vehicles need the most servicing and the actual downtime each vehicle is experiencing. When you know which vehicles are consistently taken off the floor for servicing, you’ll be able to tell how your productivity is affected.
Remember, when you need to remove a vehicle off the warehouse floor because of repairs, the rest of the fleet has to make up for that gap. This affects the efficiency of the entire warehouse. Deliveries may be late and customers will be unhappy.
And you’ll be able to see those affects in your bottom line.
Gauge your servicing costs for each unit to see which vehicles are causing the most downtime. With this information, you can decide whether those vehicles need to be replaced.
Understanding Why Your Tires Are Wearing Out
You may think that having to replace tires on your fleet vehicles is an unavoidable expense. After all, your equipment isn’t going to go anywhere (literally) without their tires.
But did you know there are actually ways to slow down the deterioration of vehicles’ tires? The way your trucks are driven affects how quickly the tires wear out. This means you may be able to save on tire replacement costs by making a few small adjustments to the way operators drive the trucks.
If the vehicles in your fleet are driven in a way that’s not optimal for the tires, they will likely wear out faster than expected — resulting in higher unit costs for your warehouse.
Does your team:
- Drive the vehicles too fast?
- Go around sharp corners quickly?
- Drive outside over rough terrain, such as railroad tracks?
These incidences may contribute to how quickly your tires wear out. Review the routes taken on a regular basis and see if anything adds to the wear and tear of your tires. You may be able to reduce your expenses on each unit by educating your operators on driving more effectively.
Watching Out for Equipment Damage
Are your drivers and forklift operators causing needless damage to your fleet? This is a sensitive topic for many companies. They trust and value their employees, and don’t want to place unnecessary blame. We get that. Your employees are the key to your success.
However, equipment damage is a reality for many organizations. Whether it is intentional or accidental, it needs to be investigated.
One of our clients, Pacific Southwest Container, dealt with this issue. In fact, they had over $50,000 in damages for their fleet vehicles each year. It was causing the unit costs for each vehicle to spike — and they needed a way to reduce those expenses.
With our help, they installed a Gem-One telemetry system, which ensured that only authorized and properly trained personnel had access to the vehicles. This enabled them to reduce their vehicles damages by $45,000 a year.
It’s important to fully trust your employees with your equipment, but it’s also critical to find ways to avoid or reduce your damage costs. This not only lowers your overall unit cost for each vehicle, it helps to improve safety in the workplace.
Knowing Your Unit Cost Opens Up More Questions
You’re probably thinking all of this sounds great, but you don’t have the time or resources to track this information and then analyze it. That’s where we come in.
With over a decade of fleet management expertise, we run the numbers so you don’t have to.
Not only do we review your unit cost for each vehicle in your fleet, we also track 4 other key warehouse performance metrics that help our clients make better business decisions about their fleet.
Curious about what those metrics are? We’ll share them with you in our 5 Key Performance Metrics On-Demand Webinar. Not only that, we also share a KPI workbook that helps you run your actual numbers, along with a cheat sheet to help you implement those metrics into your warehouse.
Sign up for the webinar to get access to this exclusive info designed to help you lower your vehicle unit cost and improve productivity in every area of your warehouse.
If you’ve got some questions about unit cost and how it can help you improve your profitability, don’t hesitate to get in touch with us. Call us at 844-360-8217 or book a no-obligation consultation to get started.
Interested in one of our products? Give us a call at 844-360-8217 or click below to get started with a free quote now!